Do rubber extrusion lines need to use screen changers?
In the rubber extrusion line, the application of screen changer (Screen Changer) needs to be based on specific process requirements, raw material characteristics and product quality requirements. The following is a detailed analysis:
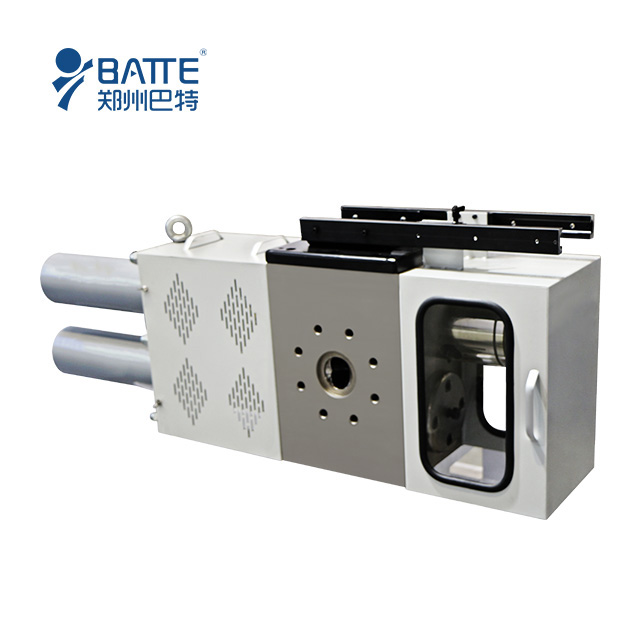
Rubber extrusion line whether to judge the need for screen changer based on
1. must be equipped with screen changer scenarios
Raw materials with high content of impurities: such as recycled rubber, scrap tire powder and other recycled materials, or carbon black filling amount of > 50phr formula.
Strict quality requirements for products:
Automotive industry: sealing strips and shock absorbing pads need to be certified by ISO/TS 16949, with surface defect rate ≤ 0.5%.
Medical industry: rubber catheters need to comply with ISO 10555 standards, inner wall smoothness Ra ≤ 0.8μm.
Continuous production requirements: such as 24-hour uninterrupted production of tire tread extrusion line, need to change the screen changer to achieve the screen without stopping, to avoid the loss of production capacity caused by the shutdown to clean up (a single shutdown loss up to tens of thousands of dollars).
2. Scenarios where screen changer can be omitted
High purity of raw materials: such as new synthetic rubber (EPDM, SBR) and carbon black dispersion.
Low value-added products: e.g. common hose, rubber shoe soles with low requirements on surface quality.
Small batch test line: laboratory or R&D stage, with small amount of raw materials and controllable impurities.
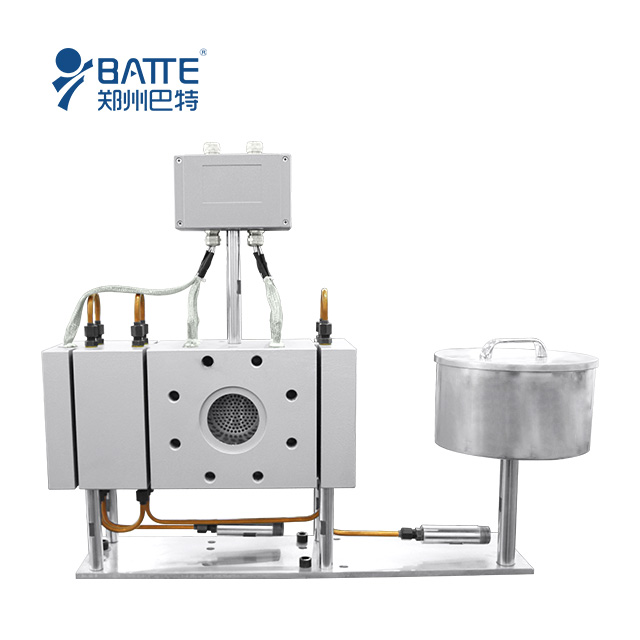
Suggestion: If the production line needs to meet one of the following conditions, it must be equipped with a screen changer:
The surface defect rate of the product is required to be ≤1%;
The impurity content of the raw material is >0.5%;
The duration of continuous production is >8 hours/day.
Email: sale@meltpump.com
WhatsApp: +86 158 3833 1071