Thermoplastic extruder screen changer in the plastics processing industry applications
Thermoplastic extruder screen changer in the plastics processing industry is widely used and critical, its core function is to filter impurities in the molten material to protect product quality, equipment stability and production efficiency. The following are the specific application areas and advantages of the analysis:
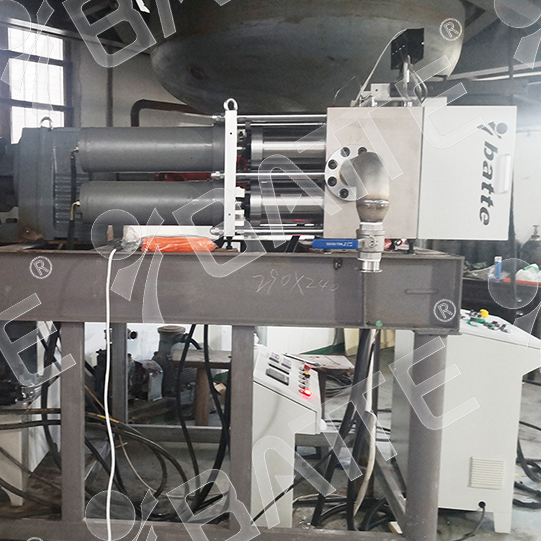
First, the core application areas
Pipe and profile production
Function: Filtering metal chips, gel particles and other impurities in the plastic melt to ensure uniformity of pipe wall thickness. For example, after an enterprise adopts double-column screen changer, the thickness deviation of PVC pipe is reduced from 5% to less than 1%, and the mold life is extended by 40%.
Case: In the production of PE water supply pipe, the screen changer can intercept the dust and plastic debris in the raw material, avoiding the pits on the inner wall of the pipe, and meeting the hygienic standard of drinking water delivery.
Film and Sheet Processing
Function: Enhance the surface finish of film and reduce defects such as crystal spots and flow marks. For example, in BOPP film production, the screen changer reduces thickness deviation from 5% to less than 1% and improves optical properties by 15%.
Case: In PC optical sheet production, the screen changer filters undispersed additive particles to increase light transmission from 88% to 92%, meeting the demand of LCD backlight modules.
Granulation and recycling field
Function: In the production of color masterbatches, filtering undispersed pigment particles to ensure the uniformity of granules. After an enterprise adopts mesh belt screen changer, the color difference ΔE value of masterbatch is reduced from 3.5 to 1.2, which meets the demand of high-end injection molding.
Case: In PET bottle flakes recycling, the screen changer intercepts label paper, glue and other impurities, so that the fluctuation range of melt index of recycled material is narrowed from ±15% to ±3%, which meets the standard of food contact grade.
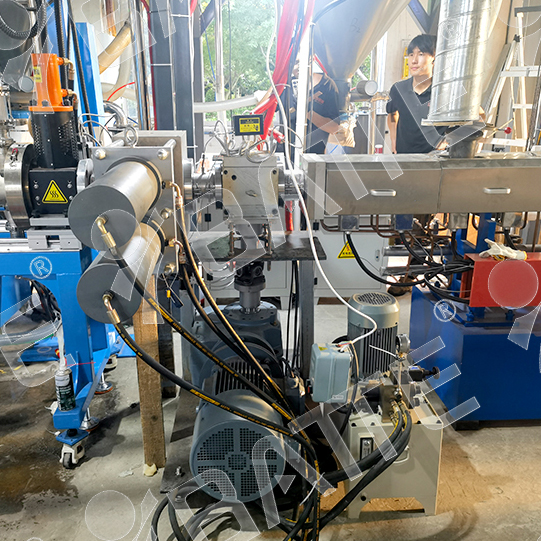
Second, technical advantages and industry value
Product quality improvement
Filtration precision: by replacing different mesh filters (e.g. 80 mesh, 200 mesh), it can intercept impurities above 0.1mm, which significantly reduces the defects such as product surface imperfections, bubbles and other defects.
Homogenization effect: the screen changer produces shearing and mixing effect on the melt, which makes the temperature, pressure and flow rate more uniform. For example, in the production of HDPE pipes, the melt homogenization increases the ring stiffness by 10% and the compression resistance is more stable.
Equipment protection and life extension
Reduced wear: Impurities are a major factor in screw and barrel wear. Screen changer can reduce the impurities into the equipment and extend the screw life by 30%-50%.
Reduced maintenance costs: Statistics of an enterprise show that after using the screen changer, the frequency of mold maintenance has been reduced from 2 times per month to 1 time per quarter, which saves more than 200,000 RMB in annual maintenance costs.
Production efficiency and cost optimization
Continuous production: double column screen changer supports non-stop screen changing, avoiding the defects of the traditional way which requires 10-15 minutes of downtime, and increasing the production capacity of single line by 15%-20%.
Reduced energy consumption: The screen changer reduces melt pressure fluctuations, stabilizes the extruder motor load, and reduces unit energy consumption by 10%-15%. For example, an enterprise's annual power saving is equivalent to reducing 42,000 tons of carbon dioxide emissions.
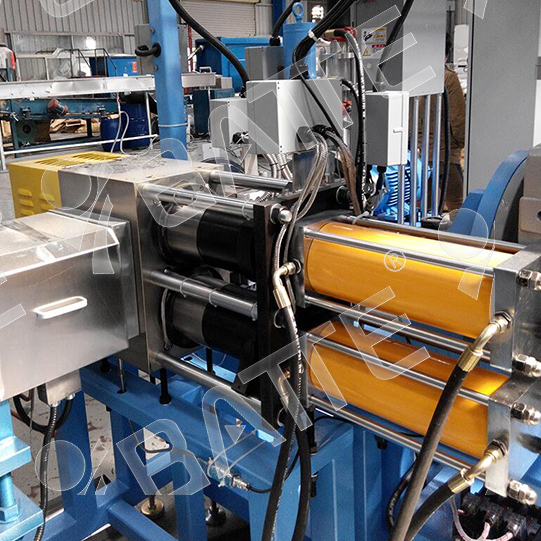
Third, Selection and adaptation suggestions
Selection according to material characteristics
High viscosity materials (such as rubber): high-pressure, wear-resistant screen material (such as nickel-titanium alloy), and configure the backwash function to extend the life of the screen.
High impurity content materials: it is recommended to use the mesh belt type screen changer, through the continuous mesh automatically discharged impurities, reducing manual intervention.
Adaptation according to the scale of production
Large-scale production: Priority is given to the double-column four-station screen changer with a high degree of automation, which supports fast screen changing (≤3 seconds) and reduces downtime.
Small scale or laboratory: manual screen changer with low cost, suitable for low-frequency production or sample testing.
Matching by process pressure
High-pressure processes (e.g. ceramic melt extrusion): a double-column backflush screen changer is required, which is constructed to withstand pressures of 40 MPa or more and ensures leak-tightness.
Low-pressure processes (such as film production): single-column screen changer can meet the needs of lower costs and ease of operation.
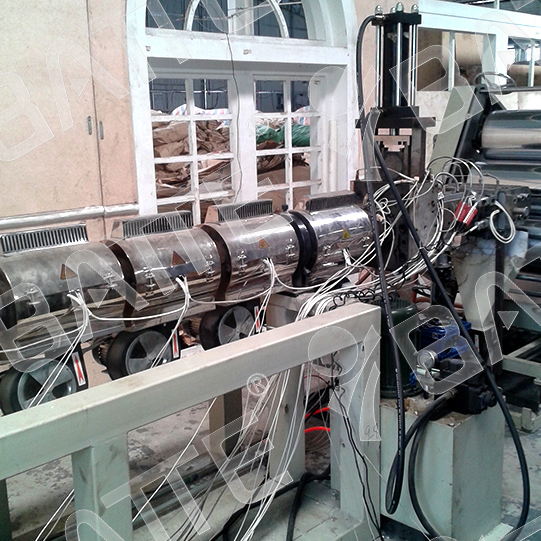
Fourth, industry trends and future direction
Intelligent control: integrated pressure sensor and PLC system, real-time monitoring of screen clogging and automatic screen changer. For example, an enterprise upgraded pressure warning response time from 10 minutes to 2 seconds, scrap rate reduced by 18%.
Energy-saving design: water-cooled seals and low-friction guides are used to reduce energy loss. The mesh belt screen changer consumes 25%-50% less energy per unit than traditional models, in line with the trend toward carbon neutrality.
Modularized structure: facilitates quick screen replacement and maintenance, shortening downtime. After an enterprise adopted the modular design, the screen changing time was reduced from 30 minutes to 5 minutes, and the production efficiency was significantly improved.
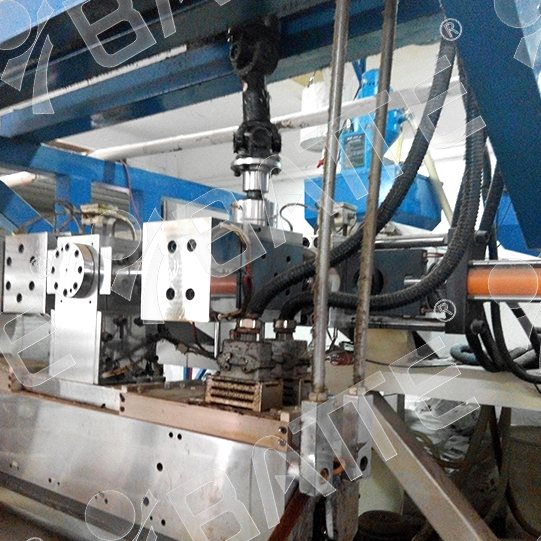
Thermoplastic extruder screen changer has become the core equipment in the plastics processing industry by efficiently filtering and stabilizing melt flow. Its application covers the whole industrial chain such as pipe, film and pelletizing, and its technical advantages include improving product quality, extending equipment life and reducing production costs. In the future, with the development of intelligent, energy-saving technology, the screen changer will further promote the transformation of the plastics processing industry to the direction of high efficiency and green.
Email: sale@meltpump.com
WhatsApp: +86 158 3833 1071